Building a Prismatic Cell Manufacturing Plant: A Comprehensive Guide
Establishing a prismatic cell manufacturing plant involves several critical steps, from initial planning and site selection to equipment procurement and quality control. This guide provides an in-depth overview of the essential phases and considerations necessary for building a successful prismatic cell manufacturing facility.
1. Planning and Feasibility Study
Market Analysis
**Demand Forecast: Analyze the market demand for prismatic cells, particularly in sectors such as electric vehicles (EVs), renewable energy storage, and consumer electronics.
**Competitive Landscape: Study the competition, including the production capacities, market shares, and technological advancements of existing manufacturers.
Financial Planning
**Investment Estimation: Calculate the total investment required, covering land acquisition, construction, machinery, and working capital.
**Funding Sources: Identify potential funding sources, such as loans, investors, government grants, or partnerships.
Site Selection
**Location: Choose a strategic location with access to essential infrastructure like transportation, utilities, and skilled labor.
**Infrastructure: Ensure the site has reliable access to electricity, water, gas, and waste disposal facilities.
2. Plant Design and Layout
Design Requirements
**Production Capacity: Determine the desired production capacity based on market demand and scalability considerations.
**Space Planning: Design the layout to optimize workflow efficiency, minimizing material handling and maximizing space utilization.
Layout Planning
**Raw Material Storage: Allocate space for storing raw materials, including electrodes, electrolytes, separators, and casings.
**Production Lines: Designate separate areas for each stage of production: electrode preparation, cell assembly, electrolyte filling, sealing, and formation.
**Quality Control: Establish laboratories and testing areas for quality control and R&D.
**Finished Goods Storage: Plan for storage of finished batteries before shipment.
3. Equipment Procurement
Key Equipment for Prismatic cell fabrication plant
1. **Electrode Preparation Equipment**
**Mixers: Prepare electrode slurry by mixing active materials, binders, and solvents. High-shear mixers ensure uniform consistency.
**Coating Machines: Apply electrode slurry onto current collectors (aluminum for cathode, copper for anode). Precise control over thickness and uniformity is crucial.
**Drying Ovens: Remove solvents from coated electrodes. Continuous or batch ovens can be used based on production scale.
**Calendering Machines: Compress coated electrodes to the desired thickness and density, enhancing electrochemical performance.
**Slitting Machines: Cut the dried and calendered electrodes into precise sizes for further processing.
2. **Cell Assembly Equipment**
**Cutting Machines: Precisely cut separators to match electrode dimensions.
**Stacking Machines: Assemble electrodes and separators into stacks. Automation ensures consistency and precision.
**Tab Welding Machines: Weld current collector tabs to electrodes. Ultrasonic or laser welding is commonly used for strong, reliable connections.
**Electrolyte Filling Machines: Inject electrolyte into assembled cells. Precision filling is essential for optimal cell performance and safety.
**Sealing Machines: Seal the cells using methods like heat sealing, ultrasonic sealing, or laser welding.
3. **Formation and Testing Equipment**
**Formation Equipment: Perform initial charge/discharge cycles to form the solid electrolyte interface (SEI) on the anode and stabilize cell performance.
**Cyclers and Testers: Test cells for capacity, voltage, internal resistance, and other key performance metrics. Automated systems can handle large volumes of cells.
**Environmental Chambers: Simulate various operating conditions (temperature, humidity) to test cell performance and durability.
4. **Safety and Environmental Equipment**
**Fume Hoods and Scrubbers: Control emissions from solvents and chemicals used in electrode preparation and cell assembly.
**Waste Management Systems: Handle and dispose of hazardous waste materials safely and in compliance with regulations.
Vendor Selection
1. **Reputation and Experience**
- Choose vendors with a proven track record in the battery manufacturing industry.
- Check references and case studies of previous installations to ensure reliability and performance.
2. **Technical Support and Training**
- Ensure vendors provide comprehensive training for operating and maintaining equipment.
- Opt for suppliers who offer robust after-sales support, including spare parts availability and technical assistance.
3. **Customization and Flexibility**
- Vendors should be willing to customize equipment to meet specific production requirements.
- Equipment should be adaptable to future changes in battery technology and production processes.
4. **Quality and Certification**
- Ensure equipment meets industry standards and certifications (e.g., CE, ISO).
- Conduct factory acceptance tests (FAT) and site acceptance tests (SAT) to verify equipment performance before final acceptance.
Procurement Process
1. **Specification Development**
- Clearly define equipment specifications based on production needs, including capacity, precision, and compatibility with other systems.
- Consult with technical experts and engineers to ensure all requirements are covered.
2. **Request for Proposal (RFP)**
- Issue RFPs to multiple vendors outlining detailed specifications, project timelines, and budget constraints.
- Evaluate proposals based on technical compliance, cost, delivery time, and vendor reputation.
3. **Evaluation and Selection**
- Create a cross-functional team (engineering, procurement, production) to evaluate proposals.
- Conduct site visits and technical discussions with shortlisted vendors to clarify any doubts and ensure alignment with requirements.
4. **Contract Negotiation**
- Negotiate terms and conditions, including payment schedules, delivery timelines, warranties, and service agreements.
- Ensure clear clauses on performance guarantees, penalties for delays, and responsibilities for installation and commissioning.
5. **Installation and Commissioning**
- Coordinate closely with vendors during the installation phase to ensure proper setup and integration of equipment.
- Perform rigorous testing and calibration to verify equipment performance and compliance with specifications.
- Provide comprehensive training to operators and maintenance staff.
4. Workforce Recruitment and Training
Recruitment
**Skilled Labor: Hire experienced engineers, technicians, and quality control specialists who are knowledgeable about battery manufacturing processes.
**Support Staff: Employ administrative, logistics, and maintenance personnel to support plant operations.
Training Programs
**Technical Training: Provide in-depth training on equipment operation, safety protocols, and quality control procedures.
**Continuous Improvement: Implement ongoing training programs to keep the workforce updated on the latest technologies and best practices in battery manufacturing.
5. Quality Control and Assurance
Quality Management System (QMS)
**Standards Compliance: Establish a QMS that complies with industry standards (e.g., ISO 9001) to ensure consistent product quality.
**Documentation: Maintain thorough documentation of all processes, from raw material inspection to final product testing.
Testing and Inspection
**Raw Material Testing: Conduct rigorous testing of incoming materials to ensure they meet specified quality standards.
**In-Process Inspection: Implement real-time monitoring and inspection at various stages of production to identify and address defects early.
**Final Product Testing: Perform comprehensive testing of finished cells for performance, safety, and durability.
6. Environmental and Safety Considerations
Environmental Management
**Emissions Control: Implement systems to control emissions from solvents and chemicals, ensuring compliance with environmental regulations.
**Waste Management: Develop procedures for the safe disposal and recycling of hazardous waste materials.
Safety Protocols
**Safety Training: Provide regular safety training to all employees, emphasizing the importance of following safety protocols.
**Emergency Response: Establish emergency response plans and conduct regular drills to prepare for potential incidents.
Conclusion
Building a Prismatic cell fabrication line is a complex yet rewarding endeavor that requires meticulous planning, strategic investment, and a commitment to quality and safety. By following this comprehensive guide, businesses can establish a state-of-the-art facility capable of producing high-performance prismatic cells to meet the growing demand for advanced energy storage solutions. With careful execution and continuous improvement, a prismatic cell manufacturing plant can become a cornerstone of innovation and sustainability in the battery industry.
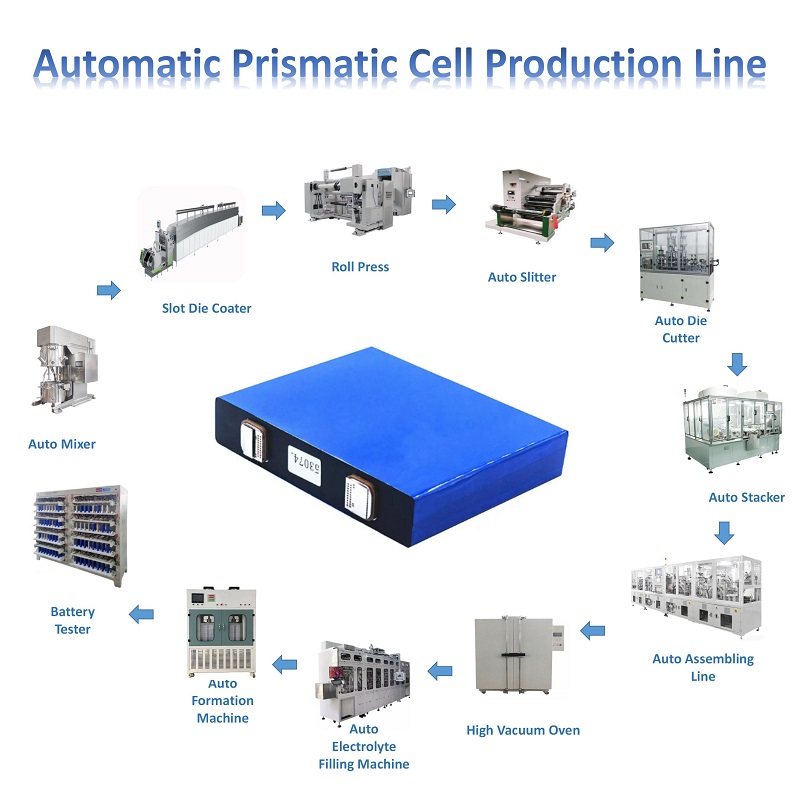