Lithium Cell Production Line: An Overview
The production of lithium-ion cells involves several intricate processes, each requiring specialized equipment and meticulous attention to detail. Here's a detailed look at the key stages of a lithium cell production line, including the advantages and challenges at each stage.
Key Stages of Lithium Cell Production
1. Electrode Manufacturing
Mixing
-
Purpose: Create a uniform slurry of active materials, binders, and conductive agents.
-
Equipment: High-shear mixers, planetary mixers.
-
Process: The materials are mixed in a solvent to form a homogeneous slurry.
Coating
-
Purpose: Apply the slurry to current collector foils (aluminum for the cathode, copper for the anode).
-
Equipment: Slot-die coaters, roll-to-roll coaters.
-
Process: The slurry is evenly spread onto the foil and dried to form a thin, uniform layer.
Drying and Calendering
-
Purpose: Remove the solvent and compress the electrode to the desired thickness and density.
-
Equipment: Continuous drying ovens, calendering machines.
-
Process: The coated electrodes are dried and then passed through calendering rollers to enhance mechanical properties and electrical conductivity.
2. Cell Assembly
Cutting and Stacking/Winding
-
Purpose: Shape the electrodes and assemble them with a separator.
-
Equipment: Laser cutters, die cutters, automatic stacking or battery winding machines.
-
Process: Electrodes are cut into precise shapes and stacked (for prismatic or pouch cells) or wound (for cylindrical cells) with a separator in between.
Electrolyte Filling
-
Purpose: Introduce the electrolyte into the cell.
-
Equipment: Vacuum filling machines.
-
Process: The electrolyte is injected into the cell under vacuum to ensure complete wetting of the electrodes.
Sealing
-
Purpose: Seal the cell to prevent leakage and contamination.
-
Equipment: Heat sealers, ultrasonic welders.
-
Process: The cell casing is sealed to encapsulate the electrolyte and electrodes.
3. Formation and Aging
Formation
-
Purpose: Activate the cell by charging and discharging it under controlled conditions.
-
Equipment: Formation chargers.
-
Process: The cell undergoes several cycles of charging and discharging to form a stable solid electrolyte interface (SEI) layer.
Aging
-
Purpose: Stabilize the cell's performance and detect early defects.
-
Equipment: Aging chambers, monitoring systems.
-
Process: The cells are stored for a period (days to weeks) while monitoring voltage and temperature to ensure stability.
4. Testing and Quality Control
Electrical Testing
-
Purpose: Verify the electrical performance of the cells.
-
Equipment: Cyclers, impedance testers.
-
Process: Cells are subjected to various electrical tests to measure capacity, internal resistance, and efficiency.
Safety Testing
-
Purpose: Ensure the cells meet safety standards.
-
Equipment: Short-circuit testers, overcharge testers, thermal chambers.
-
Process: Cells undergo rigorous testing for overcharging, short-circuiting, and thermal stability.
Advantages of Lithium Cell Production Line
-
High Efficiency: Automated processes enhance production speed and consistency.
-
Scalability: Roll-to-roll and continuous production methods allow for easy scaling to meet demand.
-
Precision and Quality: Advanced equipment ensures precise control over production parameters, leading to high-quality cells.
-
Innovation Integration: The production line can be adapted to incorporate new materials and technologies.
Challenges in Lithium Cell Production
-
Material Handling: Sensitive materials like lithium and electrolytes require careful handling to prevent contamination and ensure safety.
-
Process Control: Maintaining consistent quality across large batches requires precise control over all production parameters.
-
Cost: High initial investment in specialized equipment and technology.
-
Safety: Ensuring the safety of workers and the environment while handling reactive and potentially hazardous materials.
Development Challenges
-
Improving Energy Density: Research into new materials and electrode designs to enhance the energy density of cells.
-
Reducing Costs: Developing more cost-effective production methods without compromising quality.
-
Enhancing Safety: Innovations in materials and cell design to improve the inherent safety of lithium-ion batteries.
-
Sustainability: Addressing environmental concerns related to the extraction of raw materials and the recycling of used batteries.
Conclusion
The production line for lithium-ion cells is a complex and sophisticated process involving multiple stages and specialized equipment. While there are significant advantages in terms of efficiency, scalability, and quality, there are also considerable challenges that need to be addressed. Continuous innovation and optimization in production processes and equipment are essential to meet the growing demand for high-performance, cost-effective, and safe lithium-ion batteries.
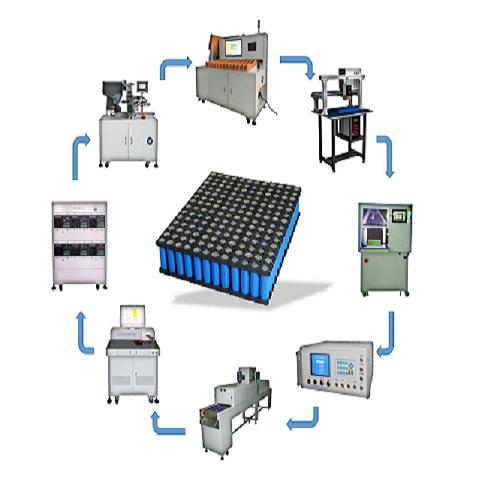